The smart Trick of Alcast Company That Nobody is Talking About
The smart Trick of Alcast Company That Nobody is Talking About
Blog Article
Little Known Facts About Alcast Company.
Table of ContentsHow Alcast Company can Save You Time, Stress, and Money.The 10-Minute Rule for Alcast CompanyOur Alcast Company PDFsThe Basic Principles Of Alcast Company Indicators on Alcast Company You Should KnowGetting The Alcast Company To WorkThe Definitive Guide for Alcast Company7 Easy Facts About Alcast Company Described
It possessed excellent toughness and machinability. There are many various other light weight aluminum alloys that can be used for casting parts. To learn which alloys would certainly benefit your tasks, contact Impro.
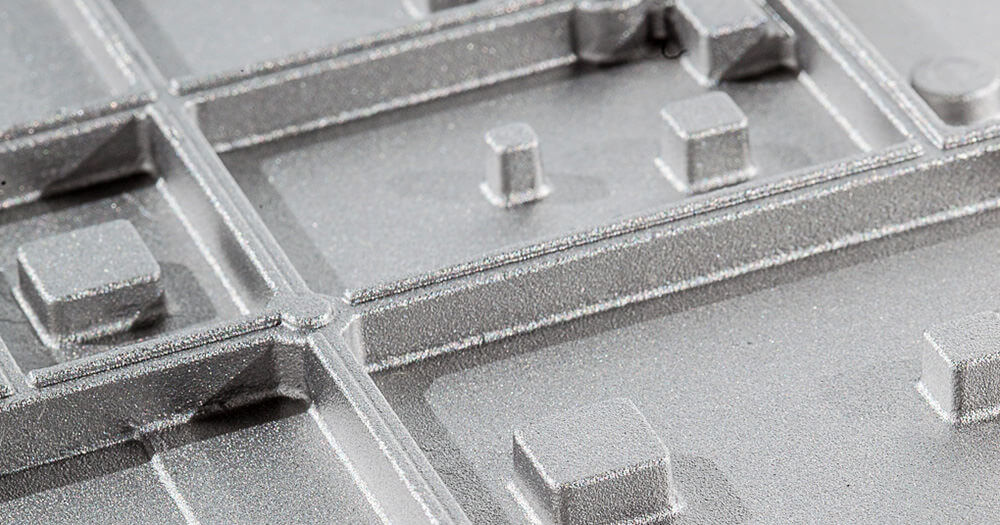
Cast light weight aluminum alloys are made by melting pure aluminum and integrating it with various other steels while in fluid kind. After that the mix is put right into a sand, pass away, or investment mold and mildew. After solidification, the metal is removed from its mold. At this stage, it remains in either its last form or as a billet or ingot for more handling.
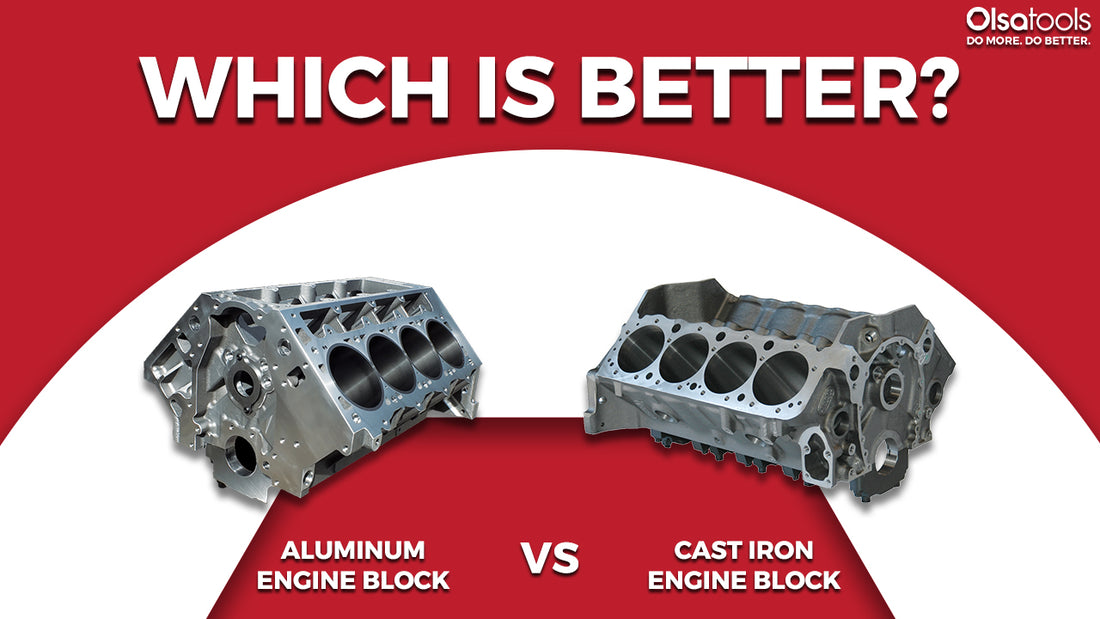
There are many minor differences in between wrought and cast light weight aluminum alloys, such as that cast alloys can consist of a lot more substantial quantities of various other steels than wrought alloys. The most significant difference between these alloys is the manufacture procedure with which they will go to provide the final product. In addition to some surface treatments, cast alloys will exit their mold in almost the precise solid type wanted, whereas functioned alloys will certainly undergo a number of adjustments while in their solid state
Alcast Company Things To Know Before You Buy
If you assume that a functioned alloy might be the very best for your job, have a look at a few of our articles that explain more regarding particular functioned alloys, such as Alloy 6061 and Alloy 6063. On the other hand, if you believe a cast alloy would be much better for you, you can discover more concerning some actors alloys in our Alloy 380 and Alloy 383 posts (coming soon).
When choosing a light weight aluminum foundry for your manufacturing demands, it's essential to research a number of variables. Among one of the most essential elements to take into consideration is the experience and proficiency of the shop. Selecting a foundry that has the best knowledge of the aluminum casting procedure, and the portfolio to show for it, aids to have a successful outcome for your job.
The Facts About Alcast Company Uncovered
Having the experience and industry expertise to engineer your castings for optimal production and high quality outcomes will simplify the job. Producing aluminum spreading calls for a facility set of procedures to attain the appropriate outcomes. When selecting a brand-new light weight aluminum shop to partner with, guarantee they have extensive industry experience and are experienced about all facets of the light weight aluminum casting process: design, production, product evaluation, and product testing.
The shop must also have a tried and tested performance history of providing outstanding products that meet or exceed customer expectations. Quality assurance needs to likewise go to the top of your list when picking an aluminum factory. By dealing with a qualified factory who adheres to the standards for quality control, you can safeguard the honesty of your product and ensure it fulfills your specifications.
The 6-Minute Rule for Alcast Company
By selecting a business that offers services that satisfy or exceed your item needs, you can be certain that your task will be finished with the utmost accuracy and effectiveness. Different components require different production techniques to cast aluminum, such as sand spreading or die spreading.
Pass away spreading is the name provided to the process of developing intricate steel components through usage of molds of the element, also recognized as passes away. It produces even more parts than any type of other procedure, with a high degree of accuracy and repeatability. There are 3 sub-processes that drop under the category of die spreading: gravity die spreading (or permanent mold and mildew spreading), low-pressure die casting and high-pressure die spreading.
Some Known Factual Statements About Alcast Company
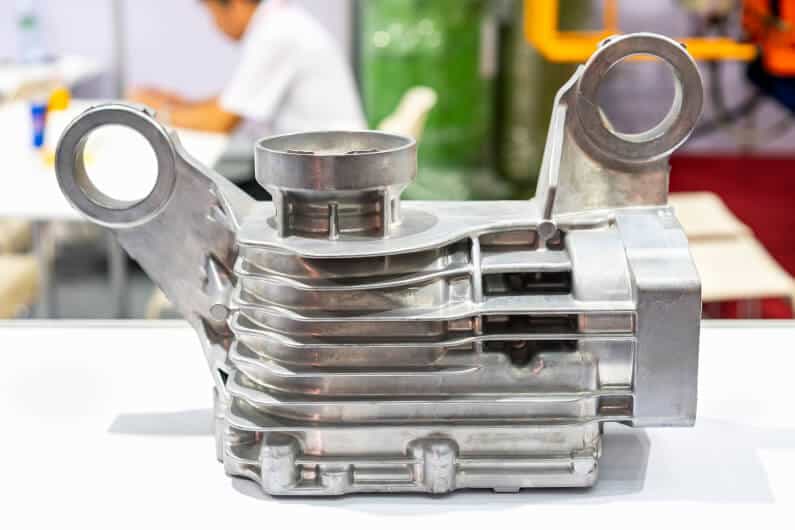
The pure metal, additionally called ingot, is included in the heating system and kept at the molten temperature level of the steel, which is then moved to the shot chamber and infused right into the die. The stress is then maintained as the metal solidifies. When the steel strengthens, the cooling process starts.
The thicker the wall surface of the component, the longer the cooling time as a result of the amount of indoor steel that also needs to cool down. After the part is fully cooled down, the die halves open and an ejection system presses the element out. Adhering to the ejection, the die is shut for the next injection cycle.
The Single Strategy To Use For Alcast Company
The flash is the added material that is cast during you can try this out the process. This need to be cut off utilizing a trim device to leave just the main part. Deburring removes the smaller sized items, called burrs, after the trimming process. The element is brightened, or burnished, to give it a smooth finish.
However, this confirmed to be an unreliable test, since the tester can reduce right into a piece and miss an area with porosity. Today, leading manufacturers make use of x-ray screening to see the entire inside of parts without cutting into them. This allows them to more accurately approve or turn down elements. To reach the completed product, there are three key alloys utilized as die spreading product to select from: zinc, light weight aluminum and magnesium.
Zinc is one of the most used alloys for die spreading due to its lower price of raw materials. Its deterioration resistance also permits the elements to be lengthy enduring, and it is one of the extra castable alloys due to its lower melting factor.
Alcast Company Things To Know Before You Get This
As stated, this alloy is one of the most generally used, yet manufactures will, at times, pick light weight aluminum over zinc due to aluminum's manufacturing benefits. Light weight aluminum is highly cost-effective and among the extra functional alloys. Light weight aluminum is utilized for a variety of various products and markets anything from window structures to aerospace products.
Report this page